Wenn in einem großen Gebäudekomplex mit über 100 Privatwohnungen Fenstergriffe ausgetauscht werden sollen, stellt nicht jeder gleich die Verbindung zur additiven Fertigung her. Doch dieses Projekt beweist aus unserer Sicht einmal mehr, dass sich die 3D-Metallverarbeitung ideal eignet, um solch komplexe und kleine Bauteile in einer überschaubaren Stückzahl herzustellen.
DMLS – ideales Verfahren für die komplexe Ersatzteilherstellung
Für unseren Kunden kam der Hauptvorteil durch die Mechanik im Inneren der Baugruppe. Auch war das additive Manufacturing kostengünstiger als Zerspanung oder Sandguss, welches der Auftraggeber zunächst für die Herstellung ins Auge gefasst hatte. Bei diesen Verfahren wären die Einmalkosten sehr hoch gewesen. Zudem hätte er sehr lange Lieferzeiten in Kauf nehmen müssen.
Kleinserienfertigung von A-Z
„Wir dagegen konnten die 200 Baugruppen innerhalb von nur 1,5 Wochen fertigstellen. Für das Projekt haben wir eine Kleinserie von 200 Baugruppen aufgelegt. Jede Baugruppe umfasste dabei 5 Komponenten,“ erklärt Thomas Hilger. „Bei der Herstellung der Baugruppe haben wir mit dem Bereich Reverse Engineering begonnen. Danach haben wir geprüft mit welchen Fertigungsverfahren wir dem Kunden den größten Mehrwert im Bezug auf Qualität und Preis bieten können. Somit kam für einen Komponenten die CNC Fertigung zum Einsatz und für die komplexen Zahnrad-Geometrien der Mechanik das DLMS oder auch SLM Verfahren im Werkstoff 1.2709 zum Zuge,“ so Hilger weiter.
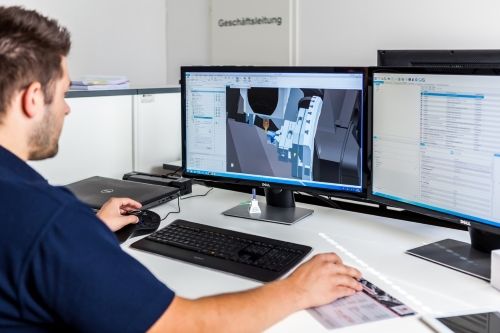
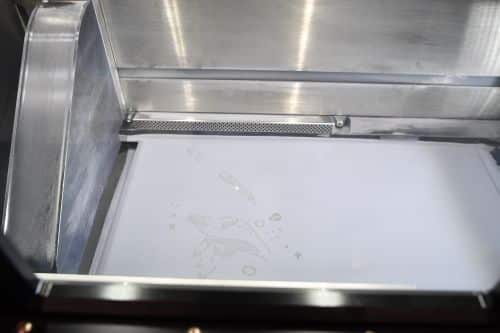
Ersatzteile müssen Belastungstests standhalten
Auf die Frage nach der besonderen Herausforderung bei diesem Auftrag antwortet sein Partner Pascal Schäfer: „Wir haben eine defekte Griffeinheit vom Kunden erhalten und mussten diese komplett nachkonstruieren. Entscheidend waren die Belastungstests. Denn die Montage sämtlicher Fenster-Griffe in über 100 Privatwohnungen ist sehr aufwendig und kostenintensiv. Deshalb muss der neue Griff unbedingt wieder eine Lebensdauer von mehr als 30 Jahren aufweisen.“
Das war auch einer der Gründe, warum der Kunde sich für LIGHTWAY entschieden habe, ergänzt Hilger: „Nachdem sich der Bauherr vergeblich bemühte, vom Hersteller der Fenster, Ersatzteile zu erhalten, suchte er nach geeigneten Alternativen. Dabei ist er auf die Vorteile der additiven Fertigung gestoßen. Überzeugt hat ihn letztlich, dass LIGHTWAY ihm die komplette Prozesskette angeboten hat. Mit allen Aufgaben angefangen beim Reverse Engineering über die Tests bis hin zur Montage. Das ist am Markt derzeit so nicht unbedingt üblich. Aber als junges und dynamisches Unternehmen sehen wir auch solche ergänzenden Arbeiten als unsere Aufgabe.“
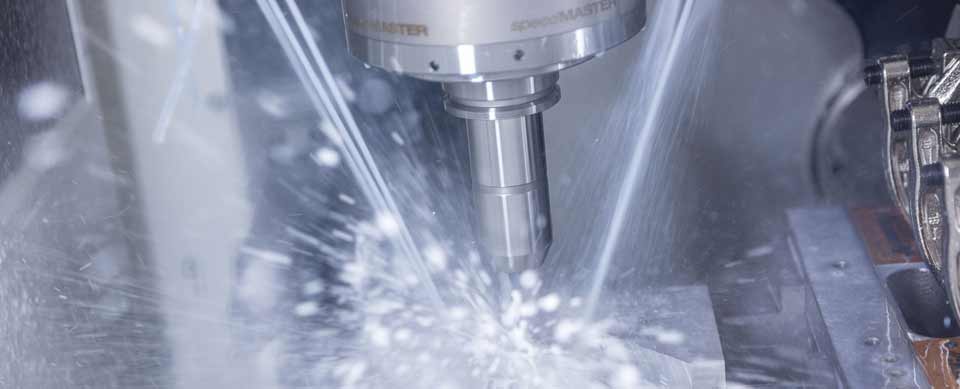
Neue Möglichkeiten durch generative Verfahren
Ganz neue Möglichkeiten eröffnen sich also durch die modernen Verfahren. Innerhalb kürzester Zeit lassen sich heute beispielsweise Mechaniken von Fenstern und Türen neu revidieren. Ersatzteile können angeboten werden, die sonst einfach nicht mehr erhältlich sind. Die einzige Option in unserem konkreten Fall wäre früher gewesen, einzelne Fenster komplett zu tauschen. Ungleich teurer und aufwändiger.
„Wir freuen uns, dass wir wieder einmal ein Projekt wie versprochen, schnell und zur vollsten Zufriedenheit eines Kunden abwickeln konnten,“ stellt Schäfer abschließend fest.
Bitte beachten Sie auch unsere News, die regelmäßig über die Entwicklung in unserem Unternehmen informieren!